Aluminum brake drums have been making a significant impact in the automotive industry, offering an innovative alternative to traditional iron brake drums. Known for their lightweight yet durable characteristics, aluminum brake drums present numerous advantages that make them a sought-after choice for modern vehicles.
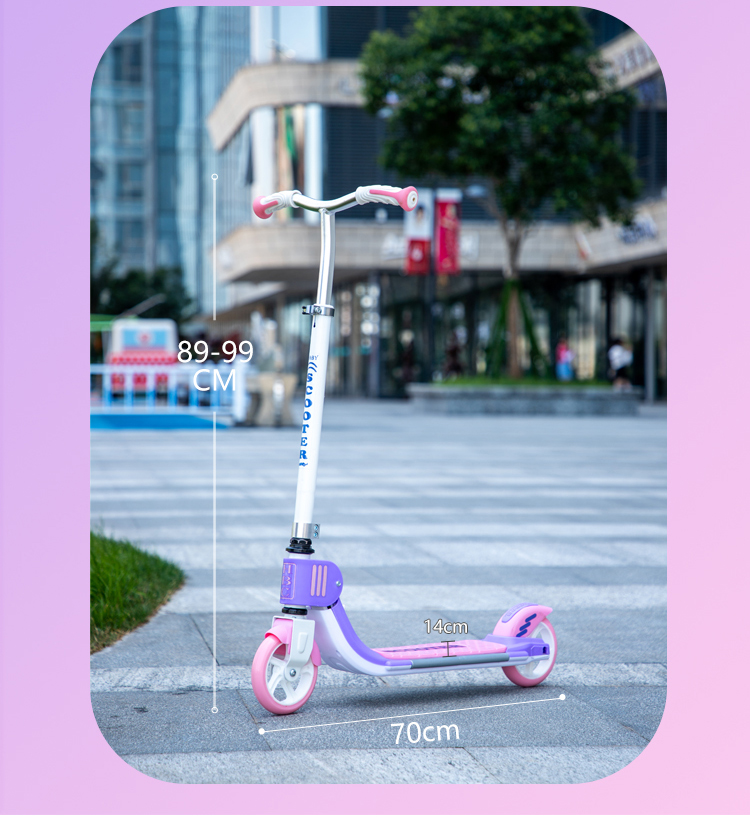
A standout benefit of aluminum brake drums is their capacity to enhance vehicle performance by reducing unsprung weight. This reduction allows for better handling and improved fuel efficiency, as the vehicle can accelerate and decelerate more easily. With less mass to rotate, wheels equipped with aluminum brake drums respond more quickly to steering input, translating to a more agile driving experience. This advantage becomes particularly apparent in performance vehicles and sports cars, where precision handling is paramount.
Beyond performance enhancements, aluminum brake drums also contribute to longevity and cost-effectiveness. Unlike iron drums, aluminum is highly resistant to rust and corrosion, factors that often precipitate the need for replacements. This durability can lead to significant cost savings over time, reducing the frequency of maintenance and replacement parts. Moreover,
the heat-dissipating properties of aluminum contribute to braking efficiency. The ability to dissipate heat more effectively than iron drums reduces the risk of overheating and brake fade, increasing the reliability of the braking system under demanding conditions.
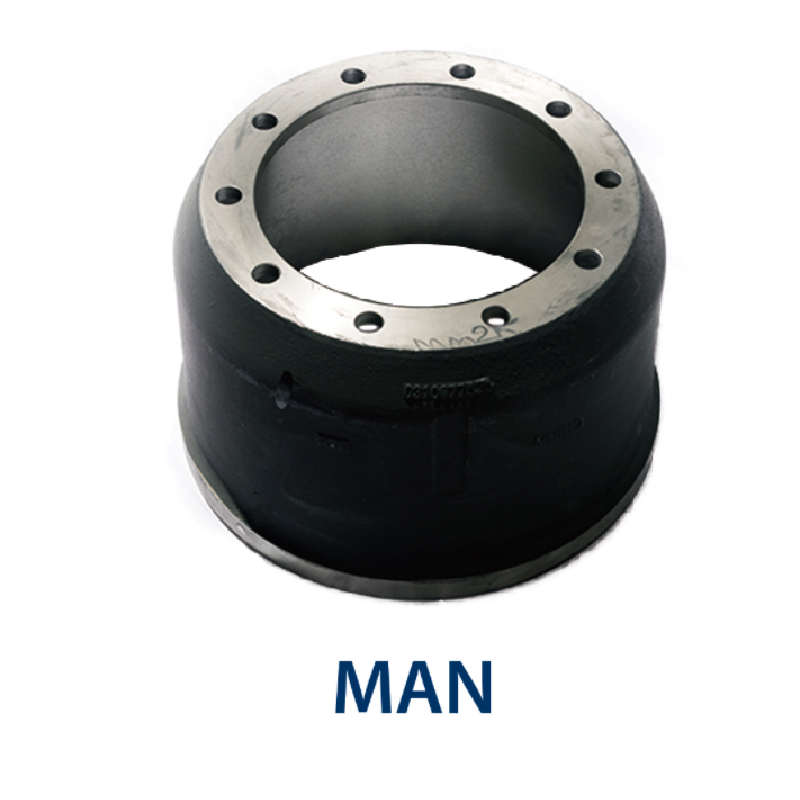
Manufacturers and automotive experts acknowledge the positive environmental implications of using aluminum brake drums. The production of aluminum components typically results in lower CO2 emissions compared to iron. Additionally, as aluminum is a recyclable material, the end-life recycling of these brake drums supports sustainable practices within the automotive sector. This ecological advantage aligns with the increasing demand for greener automotive technologies, meeting the expectations of environmentally conscious consumers.
aluminum brake drums
In terms of expertise, the industry recognizes the need for precise engineering when manufacturing aluminum brake drums. The complexity of design and the necessity for high-quality production processes are crucial to ensure the safety and effectiveness of the final product. Manufacturers invest in advanced technologies such as CNC machining and thermal treatments to achieve the structural integrity and performance standards required by automotive OEMs and the aftermarket.
For consumers, choosing aluminum brake drums also represents a commitment to cutting-edge automotive technology. The integration of this component often results in a noticeable improvement in ride quality and vehicle dynamics. Furthermore, as the discourse around vehicle electrification and hybrid technology advances, the role of lightweight materials like aluminum in brake components is expected to grow. These drums offer a valuable solution that suits the shift towards electric vehicles, where every component must be optimized for efficiency and performance.
While aluminum brake drums are not universally applicable for every vehicle type or driving condition, their advantages make them a pivotal consideration for car enthusiasts and everyday drivers alike. Automotive experts consistently recommend that vehicle owners consult with professionals to assess compatibility and ensure that installation is conducted correctly to maintain safety standards.
In conclusion, aluminum brake drums represent an advantageous innovation within the automotive sector. Their impact on vehicle dynamics, maintenance costs, and environmental sustainability positions them as a superior choice over traditional materials. As car manufacturers and consumers continue to seek innovative solutions for performance and efficiency, the role of aluminum brake drums is likely to expand, reinforcing their position as a trusted component in modern automotive design.