The automotive industry boasts an array of intricate components that are pivotal to the smooth functioning and safety of vehicles. Among these, brake drum and lining systems stand out as essential elements ensuring reliable braking performance. A deep dive into the mechanics, material composition, and industry trends associated with brake drums and linings offers a holistic view tailored for both novices and seasoned automotive experts.
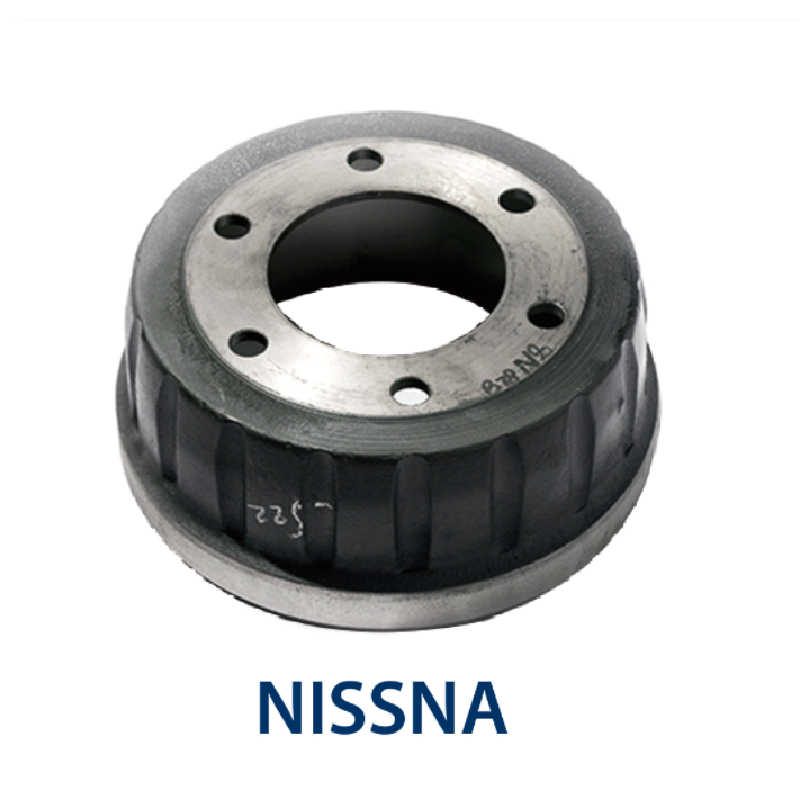
Brake drums, typically crafted from cast iron, serve as key players in drum brake systems. These components, cylindrical in nature, work by attaching to the wheel hubs. When the brake pedal engages, the brake shoes push outwards against the rotating drum, creating friction and consequently decelerating the vehicle. An understanding of the metallurgy behind cast iron reveals its popularity owing to its durability and effective heat dissipation properties, factors critical for the high-stress environment of braking systems.
The brake lining, often unsung in its role, is the real hero interplaying with the brake drum. Comprised primarily of composite materials like ceramics, semi-metallic substances, or organic elements, the brake lining acts as the frictional material. Manufacturers often face the challenge of selecting materials that offer optimal durability, noise reduction, and heat resistance. Each material choice comes with advantages ceramic linings offer minimal dust and noise, semi-metallic ones boast high durability, and organic linings are favored for their environmental friendliness.
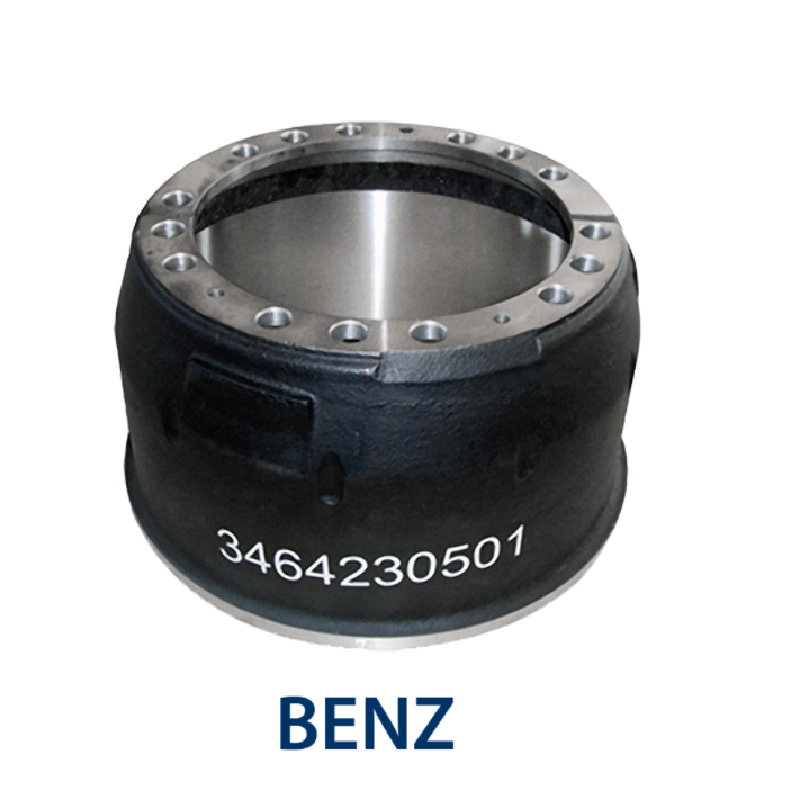
Industry insiders emphasize the dynamic relationship between brake drums and linings. Precision in the manufacturing of these components is paramount, as even minor discrepancies can lead to reduced performance or premature wear. This precision is borne out of exhaustive research and rigorous testing, underscoring the industry's commitment to safety and performance.
In recent years, innovations in brake drum and lining technologies have seen a surge. Emphasis on sustainability and environmental responsibility has nudged manufacturers to explore biodegradable lining materials and more efficient manufacturing processes that reduce waste. Forward-thinking companies in the automotive sector are leaning on cutting-edge technologies, such as 3D printing and advanced carbon composites, to revolutionize the production and performance benchmarks of brake components.
brake drum and lining
Consumer education is another critical facet. Automotive users can extend the lifespan of the brake system by adopting best practices like regular inspections, avoiding aggressive braking, and ensuring timely repairs of any related components. Such proactive measures are a testament to the rising awareness about the essential maintenance required for peak vehicle performance and safety.
For industry professionals, understanding the intricate balance of economics and engineering involved in brake systems is crucial. Cost-effectiveness in production is often challenged by the necessity for superior performance and maximum safety, driving innovation in manufacturing techniques and materials.
In the realm of expert knowledge and trust, certifications and standards play an unrivaled role. Industry standards such as those from the Society of Automotive Engineers (SAE) act as benchmarks, ensuring components adhere to stringent safety and performance criteria. This compliance not only reassures consumers but also fosters trust and establishes authority within the industry.
For those seeking to delve deeper, collaboration with reputable brands and suppliers known for their specialization in brake systems can offer invaluable insights and access to high-quality products. Such partnerships are often built on a foundation of trust, honed by verified performance records and customer satisfaction.
Brake drum and lining components may appear simple, yet they embody a depth of complexity and innovation. The continuous advancement in materials science, coupled with a consumer-oriented focus on safety and reliability, ensures that these components will remain at the forefront of automotive discourse. Stakeholders—from manufacturers to end consumers—are increasingly recognizing the integral role these products play in not just vehicle safety, but in advancing the entire automotive industry toward a more sustainable and efficient future.