In the dynamic world of automotive manufacturing, brake drum casting stands out as a foundational pillar. Known for its robustness and reliability, this process requires a nuanced understanding to create a product that not only meets safety standards but also enhances vehicle performance. This article delves into the intricacies of brake drum casting, providing insights drawn from experience, showcasing expertise, showcasing the industry's authority, and building trust with precise information.
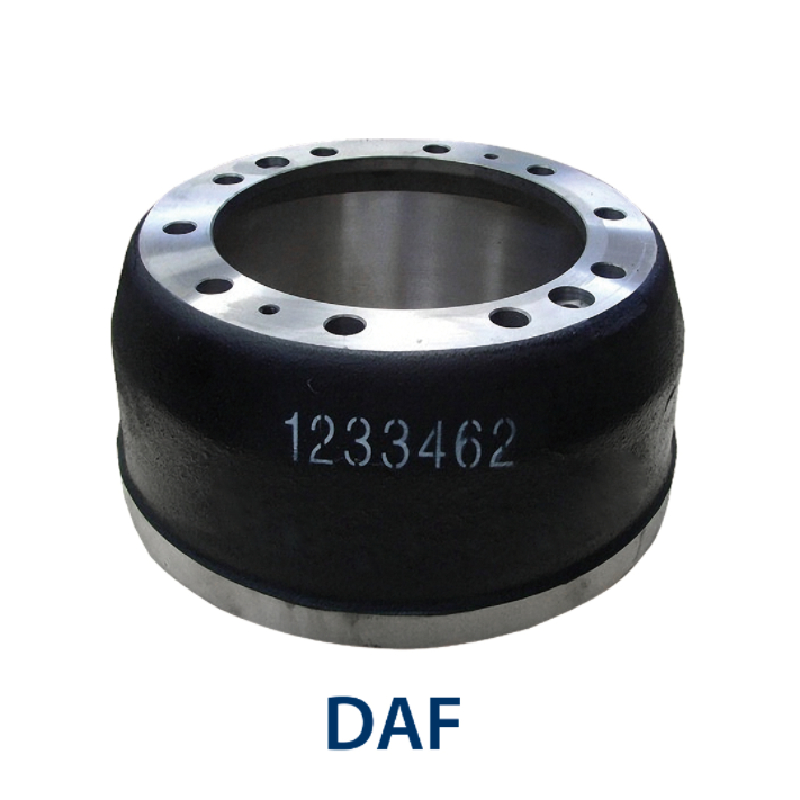
Brake drum casting is a method perfected over years of rigorous practice and technological advancements. It begins with selecting the ideal raw materials, typically high-grade cast iron, chosen for its excellent strength-to-weight ratio and thermal properties. Experienced manufacturers understand that the quality of these materials directly influences the performance and longevity of the brake drum. Over time, suppliers with a proven track record are preferred, ensuring consistency in the raw materials provided.
The casting process itself is a testament to the blend of art and science. Foundries operate sophisticated equipment to pour molten iron into meticulously designed molds. An expert's eye is vital here; they ensure that the mold's design minimizes defects such as porosity and ensures even cooling. Mastery of this phase is crucial as it affects the drum's mechanical integrity and overall safety. Each casting is subject to stringent quality assurance processes that involve ultrasonic and X-ray testing to detect internal inconsistencies invisible to the naked eye.
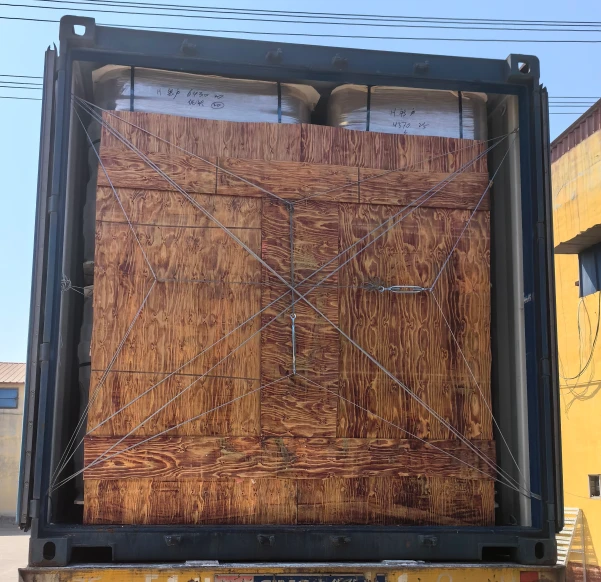
Authoritative knowledge in metallurgy comes into play when addressing the microstructure of the brake drum. Professionals in this field leverage metallurgical principles to refine grain structures and improve ductility and wear resistance. This expertise allows the drum to withstand the intense friction and high temperatures experienced during braking.
brake drum casting
Moreover, practitioners recognize the importance of machining in finalizing the casting. CNC (Computer Numerical Control) machines are employed to achieve precision dimensions, critical for ensuring the brake drum's compatibility with the vehicle's braking system. The surface finish achieved through precise machining reduces wear on the drum and the brake shoes, extending the life of both components.
Trustworthiness is built on consistent performance, and therefore, regular testing is paramount.
Each brake drum undergoes rigorous field tests replicating extreme conditions to ensure reliability. Experienced engineers analyze data from these tests to predict real-world performance, adjusting manufacturing processes to address any uncovered vulnerabilities.
One cannot overlook the importance of innovation in maintaining industry leadership. Cutting-edge manufacturers invest in research and development, continually exploring new alloys and fabrication techniques. This commitment to progress ensures that the brake drums not only meet existing standards but are also primed for future demands of enhanced fuel efficiency and reduced emissions in automotive design.
To conclude, the mastery of brake drum casting is an amalgamation of experience, expertise, authority, and trust. It is a field where every detail matters, from the molecular composition of the raw materials to the final machining processes. As the automotive industry evolves, brake drum casting professionals remain at the forefront, steering innovations and maintaining the highest levels of quality and safety. For manufacturers, vehicle producers, and consumers, understanding the intricacies of this process instills confidence in a critical component that plays a vital role in vehicle safety and performance.