Designing a brake drum forge can be both an art and a science, requiring a deft combination of traditional craftsmanship and modern engineering principles. Achieving a universal and authoritative approach involves a meticulous process that balances functional efficiency with safety and sustainability. This article delves into the nitty-gritty of brake drum forge design, embodying years of expertise and practical experience to create a reliable guide for both hobbyists and professional smiths.

A brake drum forge begins its life as a recycled brake drum, traditionally sourced from an old vehicle. These metal structures are ideal for containing and maintaining the high temperatures required for metalwork. Understanding the properties of the brake drum material is crucial for ensuring long-term performance. Typically made from cast iron, brake drums are inherently robust, heat-resistant, and capable of withstanding the rigorous demands of forging.
One critical aspect is selecting the right brake drum size. The dimensions dictate the volume of coal or charcoal that can be accommodated, influencing the forge's heat output. A larger drum may be suitable for broader projects requiring extensive heat distribution, whereas a smaller drum is apt for precise, small-scale work.
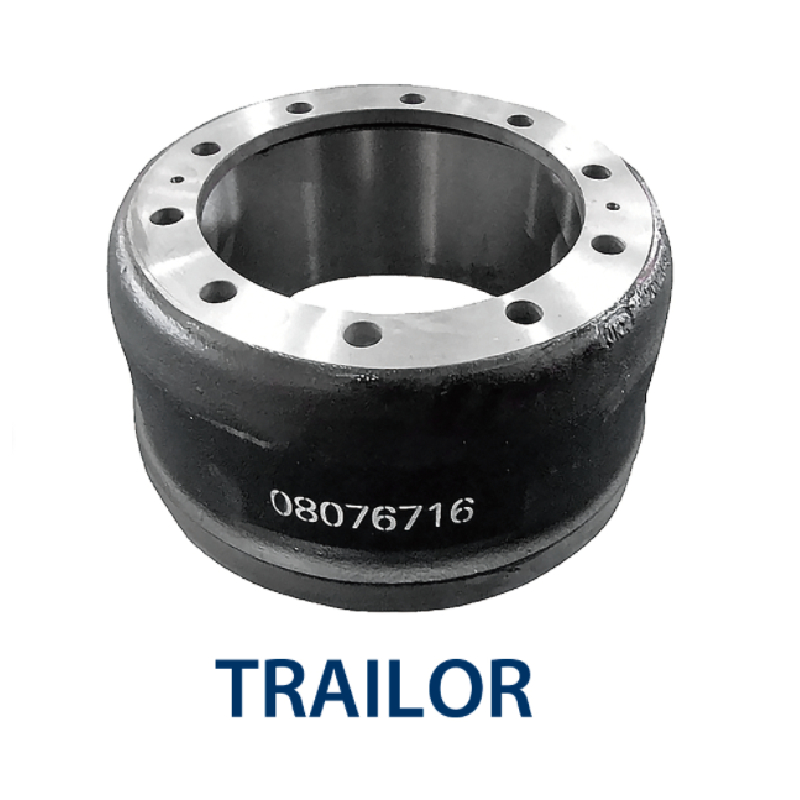
Ventilation is a pivotal component of any forge design, significantly impacting both the efficiency and safety of the operation. Proper airflow ensures consistent heating and minimizes the risk of harmful fumes. The creation of a tuyere system, which introduces air into the forge, requires a careful balance. Positioning is key; placing the tuyere too low can cause charcoal to smother the airflow, while too high can lead to incomplete combustion. Adjustable air intake systems are recommended, allowing smiths to control airflow dynamically depending on their specific needs.
The forge stand is another vital consideration. It must be stable, heat-resistant, and ergonomically designed to prevent operator fatigue. Many experienced smiths opt for metal stands due to their durability and ease of integration with the forge. However, incorporating insulating materials can help reduce heat transfer and enhance operational safety.
brake drum forge design
To harness experience and expertise in brake drum forge design, innovations in fuel efficiency and environmental impact are paramount. Transitioning from traditional coal to eco-friendly options like wood or biomass briquettes can significantly reduce the forge's carbon footprint without compromising on performance.
Another advanced technique involves integrating modern technology, such as temperature gauges and infrared thermometers. These devices provide real-time data, empowering smiths to achieve precise control over the forging conditions. Such precision not only improves the quality of the forged items but also extends the life of the forge itself by preventing overheating and material fatigue.
Expertise in the field also suggests a keen focus on regular maintenance and inspection. Frequent checks for cracks or degradation in the brake drum and supporting infrastructure can preempt potential failures. Applying protective coatings or paints designed for high temperatures can further extend the lifespan of the forge components.
Expert smiths also emphasize the importance of community and knowledge sharing. Engaging with local blacksmithing groups or online forums provides a platform for exchanging tips, troubleshooting common issues, and staying updated with emerging trends in brake drum forge design.
In conclusion, designing a brake drum forge is a journey of continuous learning and adaptation. It requires an understanding that blends practical experience with technical ingenuity, ensuring that each forge not only meets the immediate needs of its user but also stands as a testament to craftsmanship and sustainability. This holistic approach towards design embodies the principles of authority and trust—ensuring that your brake drum forge is both a tool of creation and a symbol of enduring expertise.