Creating a functional and efficient brake drum heater requires a blend of engineering expertise, hands-on experience, and a keen understanding of the unique demands of automotive maintenance. This guide delves into the key components, material selection, and practical steps necessary to construct a reliable brake drum heater, an essential tool for anyone involved in vehicle upkeep during colder months.
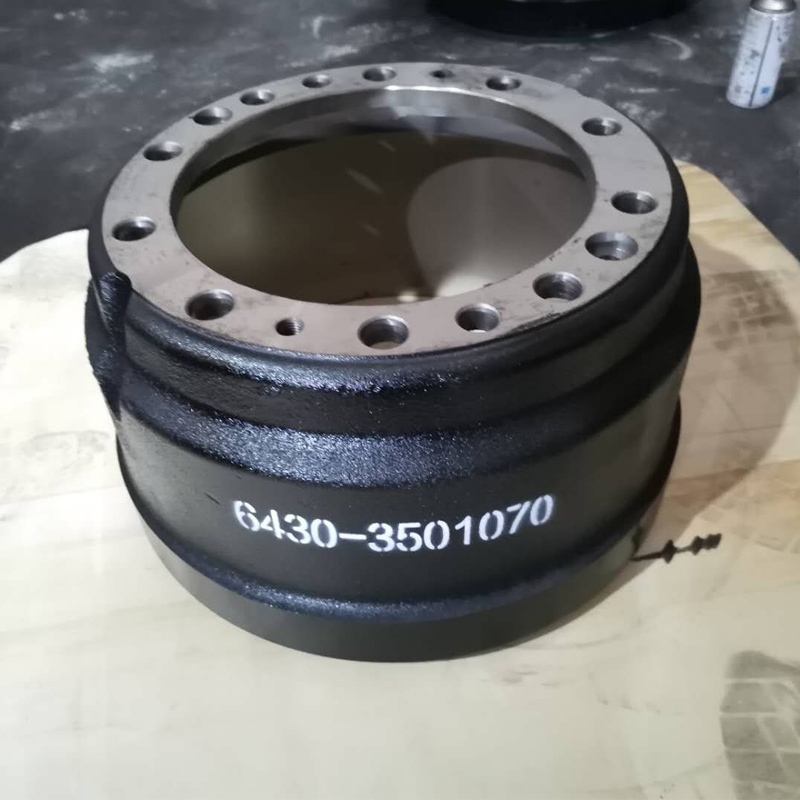
A brake drum heater is instrumental in preventing the adverse effects of cold on brake drums, such as cracking or failure due to temperature shocks. Ensuring that brake drums are adequately warmed before use can enhance vehicle safety and performance. With this in mind, the design of the heater should focus on safety, efficiency, and durability.
Material Selection and Components
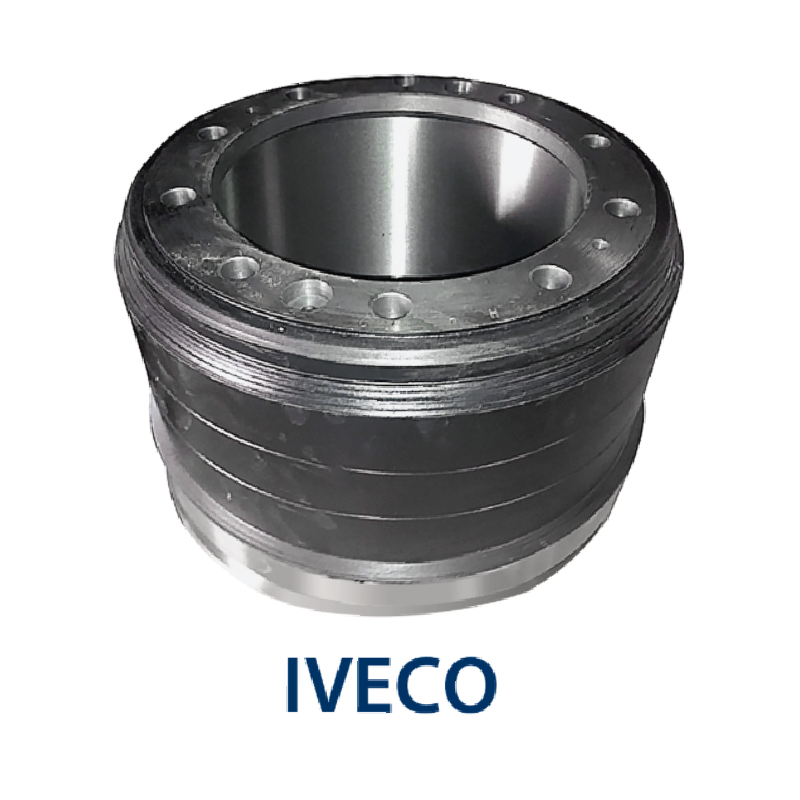
The choice of materials is paramount to the success of your brake drum heater. Stainless steel is an excellent option for the heating element due to its durability and resistance to high temperatures. Coupled with ceramic insulation, these materials ensure optimal heat retention while preventing heat loss. The design may also incorporate a thermostat to regulate the temperature and ensure it doesn’t exceed the safe limits.
Design and Construction
The design phase begins with precise calculations of the required wattage to heat the drum effectively. This can be determined by the drum's dimensions and the ambient temperature in which the vehicle operates. A common choice for the heating element is a flexible silicone rubber heater, which provides uniform heat distribution and can be easily affixed to the brake drum.
Constructing the heater involves securing the heating element to the brake drum using adjustable clamps. This allows for a snug fit, ensuring maximum contact and efficiency. The connection should include a robust electrical cord capable of withstanding environmental stresses, with a weather-resistant connector to ensure safety in various conditions.
Operational Safety
brake drum heater plans
Safety is an essential consideration. It is crucial to equip the heater with an automatic shut-off feature that activates when the desired temperature is reached. This prevents overheating and potential damage to the brake drum. Additionally, incorporating surge protection into the heater’s design will guard against electrical faults that could lead to malfunctions or hazards.
Installation and Maintenance
Installing the brake drum heater requires minimal effort but should be done with precision. First,
ensure that the drum is clean and free from debris. The heater should then be affixed according to the manufacturer's guidelines to prevent any gaps that could lead to inefficient heating. Regular maintenance checks should be a routine. Inspect the heating elements and electric fittings for wear and tear, replacing any faulty parts promptly. This will extend the life of your heater and maintain its function.
Performance Evaluation
After installation, testing the heater's performance is crucial. This involves monitoring the time it takes to heat the brake drum to the desired temperature and assessing the uniformity of heat distribution. A well-designed heater should achieve consistent results across different conditions. Any irregularities may indicate a need for design modifications or repairs.
Real-World Application
Feedback from users who have implemented similar plans highlights the practical benefits of a well-designed brake drum heater. Many have noted improvements in vehicle performance and safety during winter months. The heater's ability to eliminate warm-up times also contributes significantly to operational efficiency.
By following these guidelines, you can create a brake drum heater that is both practical and reliable. This tool not only aids in maintaining vehicle performance but also enhances safety by ensuring that brake drums function optimally regardless of external temperatures. With expertise in design and execution, the brake drum heater stands as a testament to engineering skill in addressing real-world challenges faced in automotive maintenance.