Heavy duty brake drums are an essential component in the braking systems of large vehicles, such as trucks, buses, and trailers. These components are specially designed to withstand the rigors associated with stopping heavy loads, contributing to the safety and reliability of transport vehicles. Understanding the intricacies of heavy duty brake drums can significantly enhance the performance and longevity of the braking system, making it crucial for owners, operators, and maintenance professionals to have a comprehensive understanding of their function and selection.
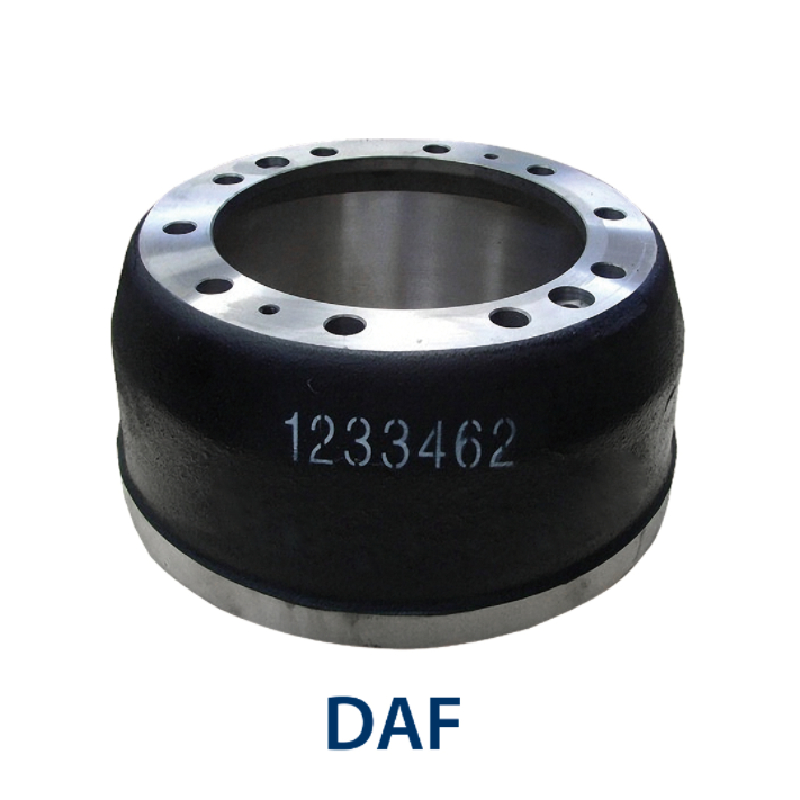
Heavy duty brake drums are often constructed from durable materials such as cast iron or steel, which provide the necessary strength to handle high levels of stress and thermal loads. This specific material composition is critical, as it allows the drum to maintain structural integrity under the extreme conditions encountered during braking. The choice of material impacts the heat dissipation capabilities and resistance to wear and tear, which are vital for ensuring consistent performance over time.
One of the key features of heavy duty brake drums is their ability to dissipate heat efficiently. During braking, friction between the brake shoes and the drum generates substantial heat. If this heat is not promptly and effectively dissipated, it can lead to brake fade, diminishing the braking ability and posing serious safety risks. Thus, high-quality heavy duty brake drums are designed to manage thermal energy efficiently, dissipating heat quickly to maintain optimal braking performance and extend the life of the brake system components.
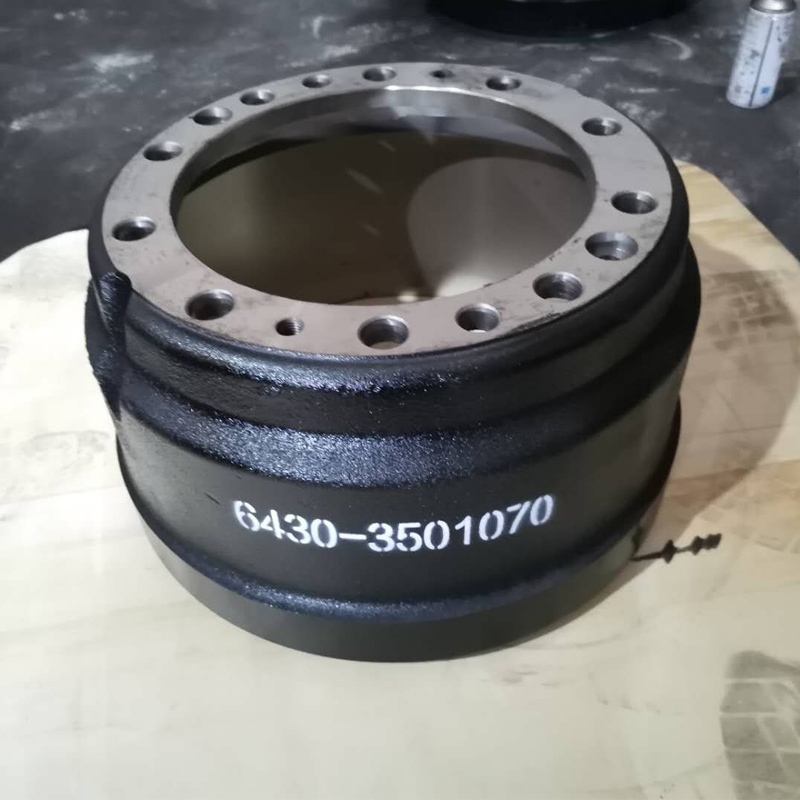
When selecting heavy duty brake drums, it is crucial to consider the specific requirements of the vehicle and its operational conditions. Factors such as vehicle load capacity, typical terrain, and frequency of use should influence the choice of brake drum. For example, vehicles operating on hilly or mountainous terrains would benefit from drums with superior heat dissipation capabilities due to the increased demand on the brakes. Similarly, regular servicing and maintenance are pivotal in ensuring that the brake drums can perform their function without compromise.
heavy duty brake drum
The installation and maintenance procedures for heavy duty brake drums should only be carried out by trained and experienced professionals. Expertise in handling these components can prevent improper fitting, which could lead to operational failures and increase the risk of accidents.
Regular inspections can identify wear and tear before it results in brake failure. This proactive approach not only extends the life of the brake drums but also enhances the overall safety of the vehicle.
Trustworthiness in selecting a supplier for heavy duty brake drums cannot be overstated. Reputable manufacturers adhere to stringent standards and rigorous testing protocols to ensure that their products meet performance and safety regulations. It is advisable to choose products from manufacturers with a proven track record and endorsements from industry authorities, which can assure users of the effectiveness and reliability of the brake drums.
Investment in quality heavy duty brake drums may initially appear costly, but the long-term benefits in terms of safety, efficiency, and reduced maintenance costs justify the expense. Durable and efficient brake drums reduce the likelihood of breakdowns and accidents, contributing significantly to operational uptime. This not only enhances fleet productivity but also instills confidence in clients and end-users regarding the safety and reliability of the service provided.
In summary, heavy duty brake drums play a pivotal role in the safe and efficient operation of large vehicles. Understanding their functionality, installation, and maintenance requirements can provide valuable insights for selecting the appropriate drums for specific applications. By prioritizing quality and consistent care, stakeholders can significantly extend the lifespan of these critical components, ensuring the safety and performance of their fleets under various operating conditions. The choice of a trusted manufacturer further underpins the dependability of the vehicle's braking system, highlighting the critical interface between product reliability and operational safety.