Heavy duty brake drums are an essential component in the transportation and heavy machinery industry, playing a crucial role in ensuring vehicle safety and performance. These robust components are engineered to withstand extreme conditions, offering superior braking efficiency and reliability. The selection of heavy duty brake drums involves careful consideration of various factors to ensure optimal performance and longevity.
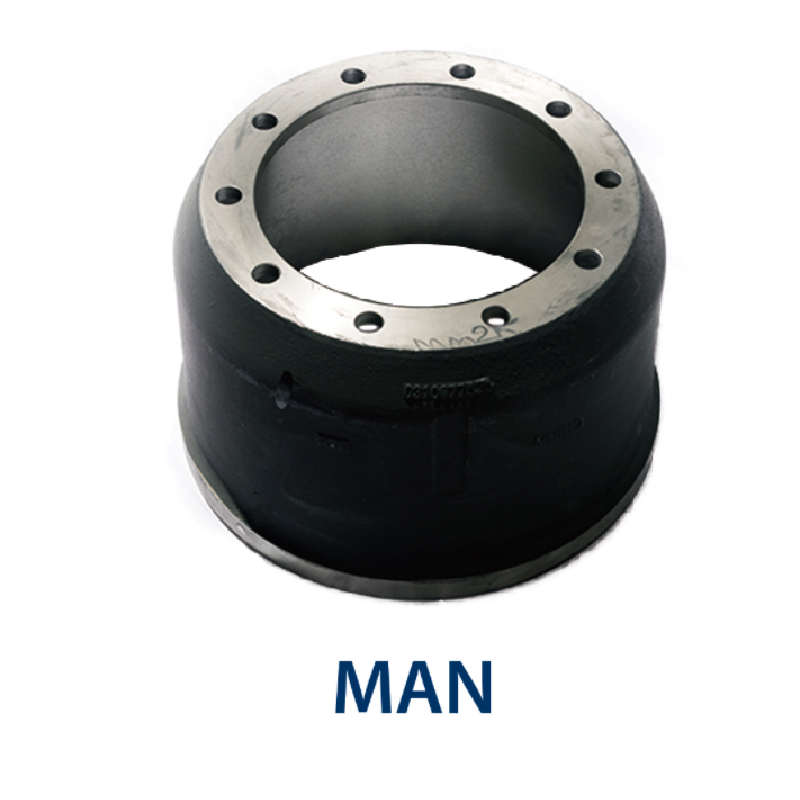
Understanding the intricacies of heavy duty brake drums begins with recognizing their construction and the materials used. Typically made from cast iron due to its excellent heat dissipation properties, these drums are designed to endure high stress while maintaining structural integrity. This material choice is pivotal; it minimizes the risk of thermal cracking and warping under extreme heat generated during braking.
The design of heavy duty brake drums is equally significant.
The symmetry and balance of the drum are critical for smooth operation. Any imbalance can lead to vibrations, noise, and uneven wear, which subsequently affects the braking system's efficiency. Manufacturers utilize advanced technological methods like computer-aided design (CAD) and finite element analysis (FEA) to optimize drum design, ensuring precision and durability.
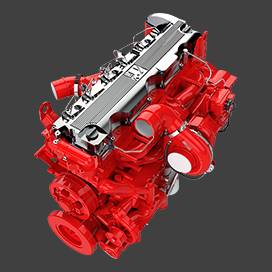
Performance testing is a cornerstone in the development of heavy duty brake drums. Rigorous testing protocols simulate real-world operating conditions, including extreme temperatures and varying loads, to evaluate the drum's performance and durability. These tests are vital in certifying that the drums meet industry standards and specifications. Endurance testing, thermal testing, and fatigue testing are some of the standard procedures that a drum undergoes to ensure it can handle the rigors of heavy-duty applications.
heavy duty brake drums
Maintenance and inspection are crucial practices for prolonging the life of heavy duty brake drums. Regular checks for signs of wear, such as scoring, cracking, or excessive rust, are essential for preventing failure. Additionally, ensuring the brake linings are compatible with the drum material and thickness is important to maintain performance standards. Employing proper maintenance protocols not only enhances safety but also optimizes the investment in these critical components.
The authority of manufacturers in the heavy-duty brake drum market often hinges on their commitment to innovation and quality assurance. Leading brands dedicate extensive resources to research and development, focusing on new materials and manufacturing processes that enhance performance and sustainability. These manufacturers often collaborate with industry regulators to help shape safety standards and contribute to the overall advancement of brake technology.
In choosing heavy duty brake drums, it's vital to consider the reputation and expertise of the manufacturer. Established companies with a proven track record in producing high-quality brake systems are more likely to offer reliable products. Moreover, looking for certifications from recognized industry standards organizations can further assure the buyer of the product’s quality and safety.
In conclusion, heavy duty brake drums are indispensable to the safety and efficiency of heavy vehicles and machinery. The choice of material, design, and adherence to rigorous testing standards play significant roles in their effectiveness and dependability. By prioritizing high-quality manufacturing and regular maintenance, these components can meet the demanding needs of the industry and reflect the expertise and authority of their manufacturers.