Brake drums are often overshadowed by more modern braking technologies, yet they remain crucial in automotive engineering, particularly for older models and larger vehicles like trucks. Understanding how brake drums work involves an intricate look at mechanics, materials, and their roles in both performance and safety. For those familiar with the sensation of slowing down a vehicle smoothly, brake drums are the unsung heroes behind that feeling.
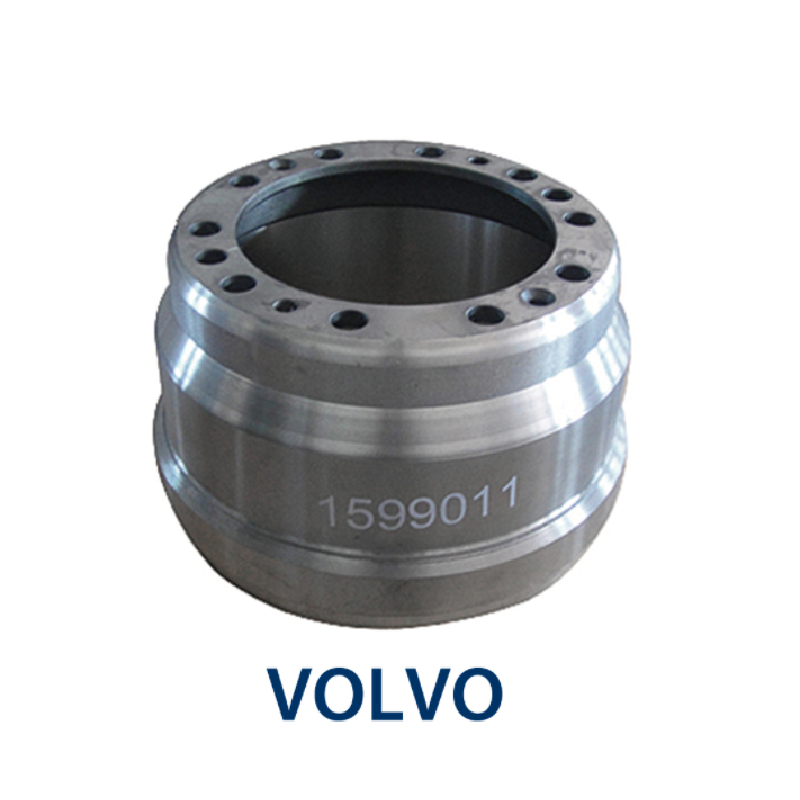
At the heart of a brake drum’s functionality is friction. The system operates through a relatively straightforward principle but involves a complex interaction of components to achieve reliable braking. When the brake pedal is engaged, hydraulic pressure is increased within the brake lines, pushing a set of brake shoes outward against a rotating drum attached to the wheel. This contact between the shoes and the drum generates friction, which converts the vehicle’s kinetic energy into thermal energy, thereby slowing down the wheel's rotation and, ultimately, the vehicle itself.
Friction materials in brake shoes are pivotal in this process. Typically, they are made from a high-strength composite designed to endure high temperatures and pressures without excessive wear. The choice of material here is critical, as it affects not only stopping power but also noise production and longevity. Apart from the ubiquitous asbestos used in early designs, modern brake shoes employ organic, semi-metallic, or ceramic composites that marry durability with reduced environmental impact.
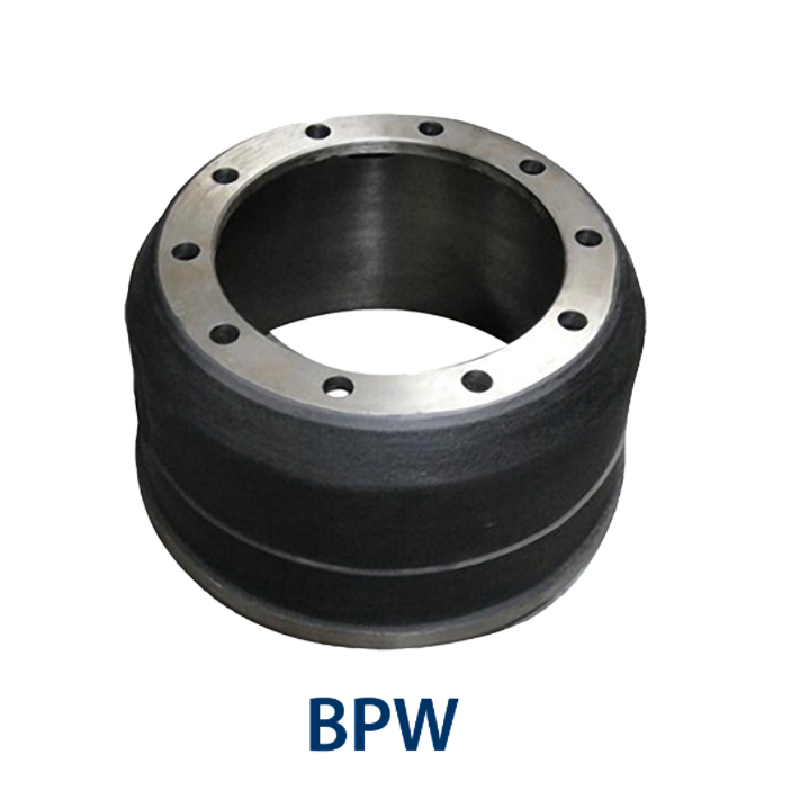
The drum is generally made from iron, chosen for its excellent heat dissipation properties—crucial since excessive heat can dramatically reduce braking effectiveness. Iron also offers the needed strength to withstand the stress of repeated use over many thousands of miles. The design of the drum often features ventilation holes or fins to promote heat loss, increasing reliability and performance consistency.
A notable advantage of brake drums is their self-energizing feature. As the shoes press against the rotating drum, they naturally generate a wedging action. This phenomenon enhances the braking force with less pedal effort compared to other systems such as disc brakes, which do not benefit from this self-energizing effect. In heavy vehicles where stopping force requirements are multiplied, this characteristic is invaluable.
how do brake drums work
While brake drums bring solid advantages, they also face challenges that are primarily related to maintenance and heat management. Continuous high-temperature operation can lead to 'brake fade', a condition where the braking efficiency drastically drops due to heat build-up. This underscores the importance of regular maintenance and inspections. To maintain optimal performance, one must ensure that both brake drums and shoes are checked for wear and deformation periodically. Drums should ideally be resurfaced or replaced once they exceed wear limits or show signs of cracking.
Moreover, environmental conditions pose another challenge. Musky environments can accelerate corrosion, leading to drum deterioration and affecting performance. Protective coatings and using quality, corrosion-resistant materials can mitigate this risk significantly.
In contemporary use, brake drum systems continue to see integration in vehicles where weight distribution and utility outweigh the need for rapid performance or in scenarios where cost-efficiency is desired. Despite the burgeoning popularity of disc brakes, the drum brake's mechanical simplicity translates to lower manufacturing costs and repairs, persistent reliability, and notable performance in specific applications.
For those maintaining older vehicles or heavy-duty transport, understanding and appreciating the function of brake drums is not merely academic but an essential aspect of vehicle safety and reliability. Mastery over this component means ensuring security in one's driving experience and a grasp on the enduring legacy of brake drum technology. This enriches the conversation around automotive technology, merging history with the present need for safety and performance.