When it comes to understanding vehicle maintenance, one of the crucial yet often overlooked aspects is the temperature that brake drums can reach during use. This knowledge is particularly essential for ensuring safety, optimizing performance, and extending the lifespan of brake components. Given their pivotal role in vehicle braking systems, comprehending how hot brake drums can become provides valuable insights into the design, materials, and operational limits of these components.
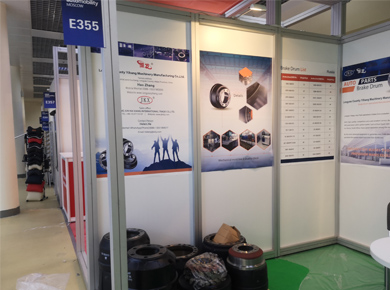
Brake drums, primarily made from cast iron for its excellent heat dissipation properties, are designed to endure and distribute the significant heat generated by friction. During typical driving conditions, brake drums can reach temperatures of 100 to 200 degrees Celsius (212 to 392 degrees Fahrenheit). However, during intense or prolonged braking, such as driving downhill or in racing conditions, the temperature can escalate rapidly, reaching levels as high as 300 degrees Celsius (572 degrees Fahrenheit) or more. This extreme heat can directly affect the braking system's efficacy, causing thermal expansion, brake fade, or even damage to the brake components if not properly managed.
These high temperatures underscore the necessity for quality materials and design precision. High-grade alloys and specialized casting techniques are employed to manufacture brake drums capable of withstanding such thermal stress. Advanced materials, like carbon composites or alloys with copper additives, are sometimes used in performance or heavy-duty vehicles to further enhance heat regulation. This attention to material science ensures the brake drums maintain structural integrity and operational efficiency under severe conditions.
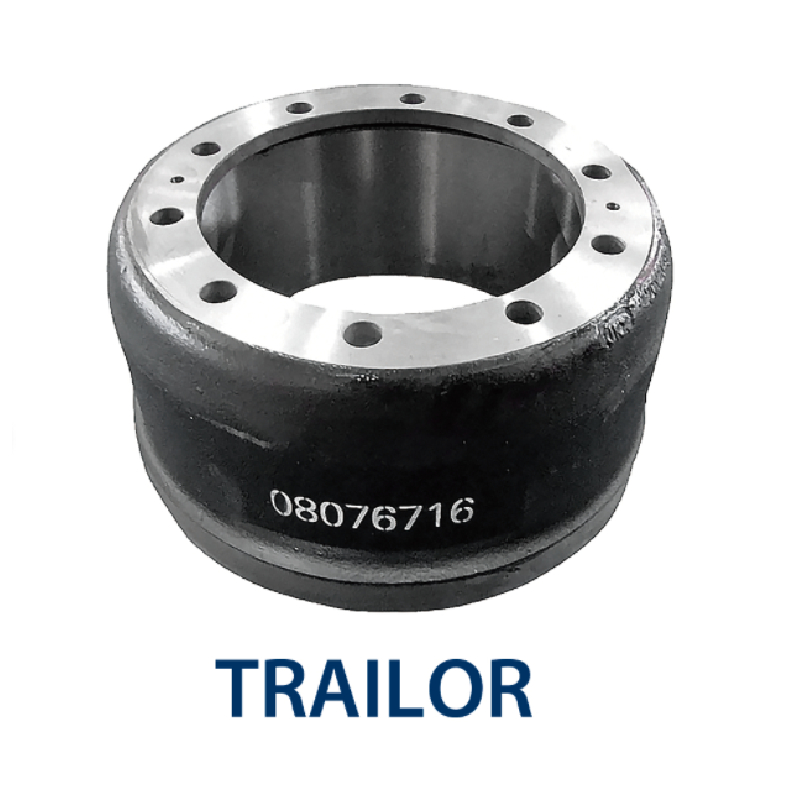
For drivers, understanding these temperature thresholds is critical in preventing potential hazards. Overheating can lead to brake fade, a condition where the braking system loses effectiveness due to the thinning film of lubricating grease and increased kinetic energy that compromise the friction between the brake lining and the drum. Recognizing the signs of overheating—such as a burning smell, decreased braking performance, or unusual noises—empowers drivers to respond promptly and appropriately.
how hot do brake drums get
Proactive maintenance is another key aspect of managing brake drum temperatures. Regular inspection of the braking system, ensuring adequate ventilation around brake components, and replacing worn-out parts can significantly mitigate the risk of overheating. Moreover, adopting safe driving practices like engine braking on long descents and avoiding abrupt stops can substantially reduce heat buildup. Consulting with automotive specialists and adhering to manufacturer guidelines further enhances the reliability and safety of brake systems.
Incorporating technological advancements, such as electronic brake monitoring systems, can offer real-time data on the performance and temperature of brake components. These systems alert drivers to potential issues, allowing for timely intervention before reaching critical temperature levels. This integration of technology not only aids in immediate risk management but also informs long-term maintenance strategies based on empirical data, enhancing the overall trust in automotive safety solutions.
Ultimately, the heat generated in brake drums is a testament to their critical function and the technological marvel they represent. Understanding their thermal dynamics not only shapes our approach to vehicle maintenance but builds a foundation of trust and reliability in personal and commercial transport. It is this blend of engineering, expertise, and practical application that ensures vehicles remain both high in performance and uncompromising in safety.