When upgrading brake performance or enhancing the aesthetic appeal of a vehicle, many automotive enthusiasts and professionals gravitate towards powder coated brake drums. This modern finishing technique promises not only improved visual appeal but also superior durability and protection compared to traditional painting methods.
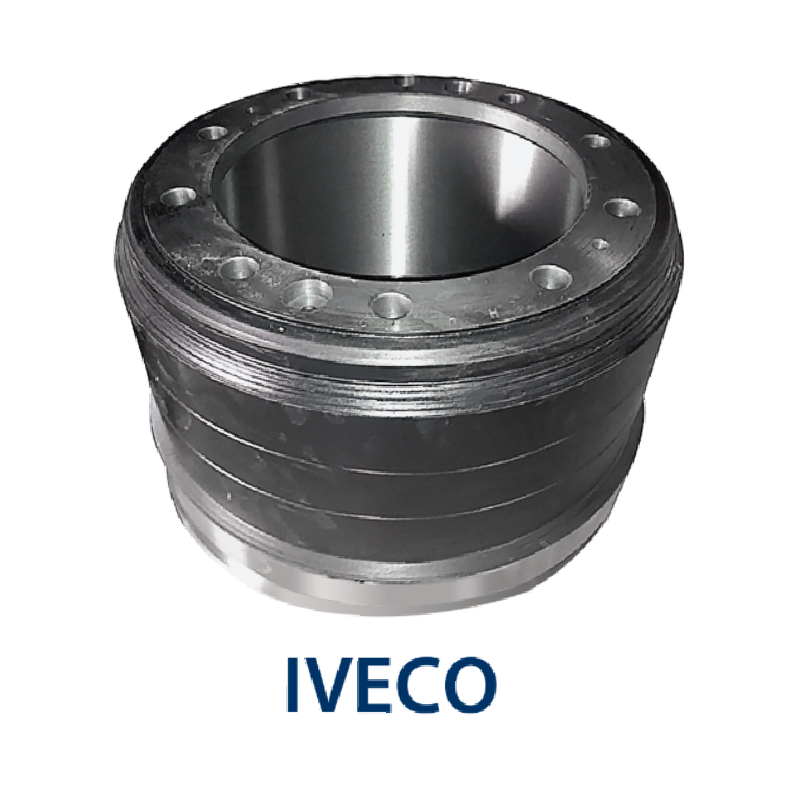
Powder coating has revolutionized the automotive parts industry with its robust offering, adding a layer of protection that extends the lifespan of brake drums significantly. Unlike conventional paint, powder coating involves applying a dry powder that is electrostatically charged before being cured under heat to form a skin. This technique ensures that the coating is uniform and adheres tightly to the surface, providing an even finish free from drips and indices of wear commonly associated with liquid paint.
A major reason enthusiasts prefer powder coated brake drums is due to their enhanced resilience against the elements. Brake drums are continually exposed to harsh conditions such as rain, road salt, dirt, and debris. A powder-coated finish acts as a shield against these elements, minimizing the risk of corrosion and rust. This extends the service life of brake drums, which in turn ensures the vehicle’s braking performance remains uncompromised over time.
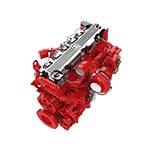
From a professional standpoint, powder coating is also favored for its environmental benefits. Traditional liquid paints often release volatile organic compounds (VOCs) into the atmosphere, contributing to pollution. Powder coating, however, contains no solvents and releases negligible VOCs, making it an environmentally friendly option that aligns with modern ecological regulations and standards. This aspect is particularly reassuring for those in the automotive industry eager to reduce their environmental footprint.
In terms of heat resistance—a crucial factor for brake components—powder coated drums excel. The curing process involves exposure to high temperatures, which enhances their resistance to the intense heat generated during braking. This stability at high temperatures means the coated surface is less likely to degrade or discolor, maintaining its visual appeal and performance efficiency over time.
powder coated brake drums
Given the demands of high-performance vehicles and the wear they inflict on components, powder coated brake drums have become a staple among automotive professionals. Their ability to maintain structural integrity and aesthetic appeal under duress makes them an invaluable upgrade. Whether dealing with everyday commuter vehicles or high-octane race cars, the need for reliability in braking systems cannot be overstated.
Powder coatings provide an advanced option to meet and exceed these demands.
In the realm of customization, powder coated brake drums offer a palette of possibilities that can match any taste or vehicle design. With a wide spectrum of colors and finishes, car owners and fabricators can achieve personalized aesthetics that enhance not just the function but also the form of their vehicles. This flexibility is particularly valuable when complete customization is a key consideration for individual or brand presentation.
Lastly, installation and maintenance ease further underscore the benefits of using powder coated brake drums. While initial installation might involve professional expertise to ensure optimal application and performance, powder coatings require minimal maintenance post-application. The robust finish withstands frequent washing, road debris, and fluctuating temperatures, reducing the need for constant upkeep or refinishing.
In conclusion, powder coated brake drums combine the best of durability, environmental responsibility, and customization flexibility. This makes them an optimal choice for anyone seeking to enhance their vehicle’s performance and appearance without compromising on quality or environmental ethos. As this method continues to gain popularity, it significantly contributes to elevating the standards of automotive component finishes, setting a new benchmark for excellence in the industry.