Choosing the right brake drum for a stud pilot system is crucial for ensuring the optimal performance and safety of heavy-duty vehicles. With an expert's eye, one can appreciate the intricate balance of engineering, material science, and practical application that goes into the modern brake drum. These components are not just about stopping power; they’re about integrating seamlessly with the entire vehicle's braking system, which is vital for large vehicles such as trucks and buses. Understanding the nuances of stud pilot brake drums can significantly enhance a mechanic's or fleet manager's ability to choose the right products, ultimately impacting vehicle performance and safety.
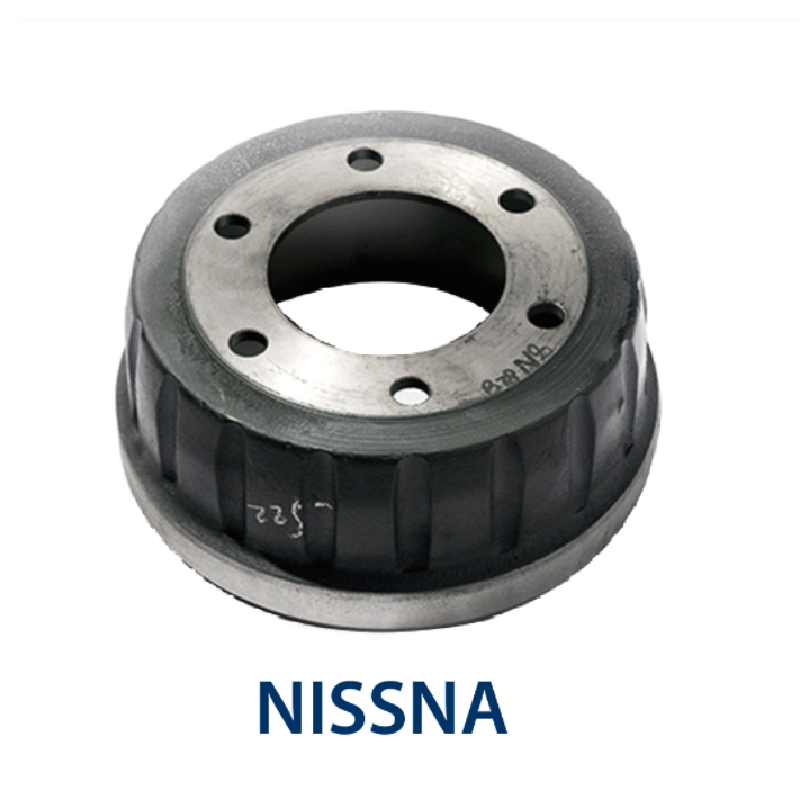
A stud pilot brake drum is designed differently from its hub pilot counterpart. The key distinction lies in how the drum is centered onto the hub. In stud-piloted systems, the studs act as the centering mechanism, guiding the drum into position. This design necessitates precise manufacturing standards, as even the slightest deviation can lead to imbalance and vibrations that compromise safety and vehicle efficiency.
Material selection is a critical aspect of brake drum design. High-quality cast iron is traditionally used for its excellent heat dissipation and durability. However, advancements in composites have introduced alternatives that are lighter yet still robust. The choice of material affects the brake drum's thermal management abilities, directly influencing the wear and tear on other braking components such as brake shoes. It's vital to consider the operational context – trucks operating in mountainous regions may require drums with superior heat management capabilities to prevent brake fade during extended descents.
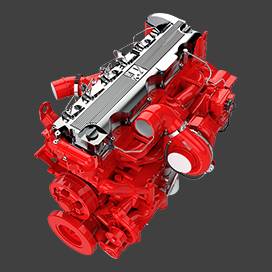
Past experiences have highlighted the importance of balancing a stud pilot brake drum correctly. Improper balance can lead to uneven wear on tires and suspension components, increasing maintenance costs and downtime. Mechanics with expertise in this area can ascertain that drums are not only balanced but also correctly aligned with the wheels. Utilizing advanced balancing machines and periodically checking alignment can extend a vehicle's operational life and ensure that every trip remains smooth and safe.
In terms of expertise, it’s essential to understand the specific requirements of different vehicle types and their operating conditions. For city buses, for instance, frequent stopping and starting put immense stress on brake systems, calling for drums that can withstand these conditions without frequent replacement. In contrast, long-haul trucks might prioritize drums that aid in fuel efficiency due to their ability to maintain lower temperatures over vast stretches of highway driving. The presence of dust shields and self-cleaning designs can be beneficial in dusty environments, protecting the brake system from particulate-induced wear.
stud pilot brake drum
Authoritative input from professionals in the field has led to the development of rigorous testing and quality assurance protocols. SAE (Society of Automotive Engineers) standards dictate specific requirements for material strength, resilience under heat, and performance during emergency stops. Being informed about and ensuring compliance with these standards is crucial for any purchasing decision, underscoring the importance of sourcing drums from reputable manufacturers known for their adherence to these benchmarks.
Trustworthiness in brake drum suppliers is non-negotiable. Reading reviews, understanding warranty terms, and evaluating supplier reputations are steps that should not be taken lightly. Transparent supply chains and certifications provide a layer of trustworthiness that helps establish long-term business relationships. Engaging with suppliers for insights and future innovations can often lend itself to strategic advantages.
Real-world experiences dictate that even the best-made brake drum will falter under inattentive maintenance. Regular inspections, combined with feedback from drivers, can identify issues early. Practical knowledge, such as listening for telltale signs of brake wear or feeling vibrations through the steering wheel, are invaluable for early diagnosis of potential problems.
Evaluating brake drum systems through a composite lens of experience, expertise, authoritativeness, and trustworthiness not only enhances the lifespan and efficacy of the component itself but also ensures the comprehensive safety and efficiency of the vehicle. Every interaction, from the mechanic's touch to the manufacturing floor, plays a pivotal role in defining the standard of safety that modern transportation demands. This exploration into stud pilot brake drums challenges us to prioritize quality and precision, ensuring that every journey is not just efficient, but also secure.