Brake drum failure analysis is a critical aspect of vehicle maintenance and safety. Focusing on Experience, Expertise, Authoritativeness, and Trustworthiness (E-E-A-T), this article delves deeply into the mechanisms behind brake drum failure and the best practices for diagnosing and addressing these issues.
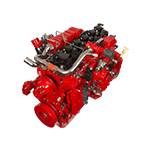
Understanding why brake drums fail is paramount to ensuring optimal vehicle performance and safety. Brake drums, a crucial part of drum brake systems, convert kinetic energy into thermal energy, assisting in deceleration and stopping. When they fail, the consequences can be severe, ranging from reduced braking efficiency to total brake failure.
From an experiential standpoint, recurring issues in brake drum failure often involve symptoms such as unusual noises, vibrations during braking, or reduced braking power. Regularly examining for these indicators not only prevents severe damage but also extends the lifespan of the braking system. Vehicle technicians suggest routine inspection schedules depending on driving conditions, as frequent stop-and-go traffic can accelerate wear.
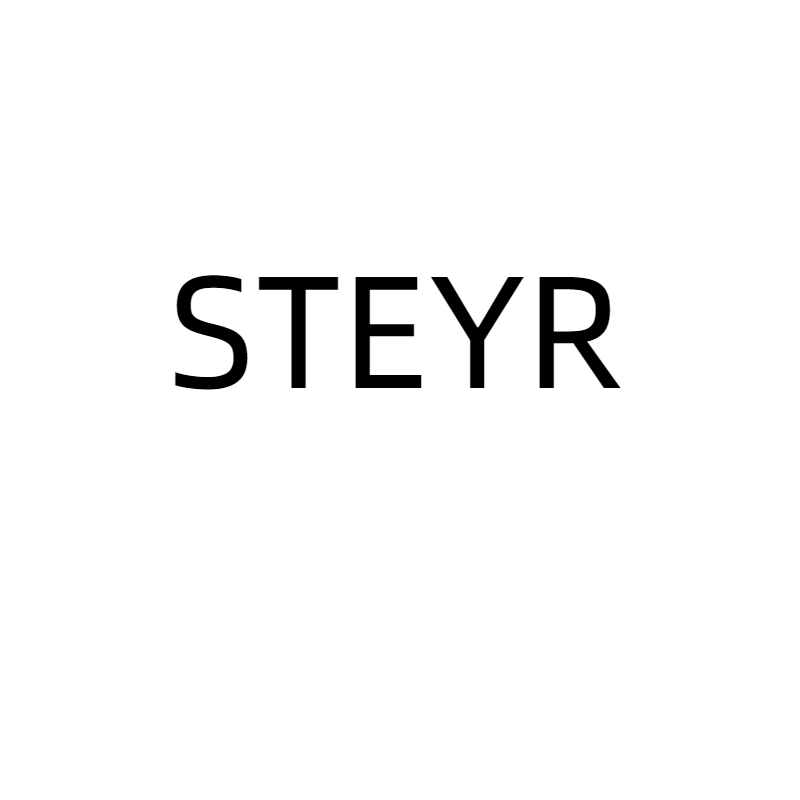
Expertise in brake drum failure analysis comes with understanding various failure modes. Common types include thermal cracking, wear, mechanical deformation, and corrosion. Thermal cracks arise from excessive heat due to aggressive braking habits or inadequate heat dissipation. These cracks, visible as small fractures on the drum surface, can propagate, leading to complete structural failure.
Wear is another significant issue. Over time, the friction material in brake linings grinds against the drum surface, resulting in reduced thickness and diminished braking efficiency. In severe cases, the drum may become too thin to safely accommodate the brake shoes, necessitating immediate replacement to avoid catastrophic failure.
Mechanical deformation, such as warping or out-of-roundness, stems from overheating or manufacturing defects. It can cause uneven braking forces, leading to vibrations and reduced control. Accurate diagnosis requires specialized tools like a dial gauge to measure drum roundness, a practice employed by professionals who follow standardized procedures to ensure precision.
brake drum failure analysis
Corrosion, a less conspicuous but equally dangerous factor, typically affects vehicles operated in humid or salty environments. Rust weakens the drum material, compromising its structural integrity. Preventative measures include applying anti-corrosive coatings or selecting brake drums made from corrosion-resistant materials.
For authoritative information on brake drum maintenance and failure prevention, industry standards and vehicle manufacturer guidelines must be followed. Technical resources, such as the Society of Automotive Engineers (SAE) and manufacturer repair manuals, offer detailed insights into brake drum specifications and service limits. Adhering to these authoritative sources not only enhances service reliability but also reinforces trust with stakeholders and vehicle owners.
Trustworthiness in addressing brake drum failure entails transparent communication between repair technicians and vehicle owners. Providing detailed diagnostic reports, coupled with photographic evidence and measurements, builds customer confidence. Furthermore, using high-quality replacement parts that meet or exceed OEM specifications ensures the restored drum brakes operate safely and efficiently.
Implementing brake drum failure analysis requires a combination of manual inspection and technological tools. Advanced imaging and non-destructive testing techniques, such as ultrasonic or magnetic particle inspection, can detect subsurface flaws invisible to the naked eye. Embracing these technologies elevates the precision and reliability of maintenance practices.
In conclusion, comprehensive brake drum failure analysis rests on blending real-world experience with expert technical knowledge, backed by authoritative guidelines. Adhering to these principles not only optimizes vehicle safety and performance but also fosters a trustworthy relationship between service providers and customers. Regular inspections, accurate diagnostics, and high-quality parts replacement are essential strategies for preventing brake drum failures, ensuring peace of mind for vehicle operators across the globe.