Crafting a brake drum forge presents a unique blend of creativity and functionality, allowing blacksmiths to harness intense heat for metalworking. With decades of expertise in metallurgy and practical blacksmithing, I delve into the intricate process of constructing a brake drum forge that ensures efficiency, durability, and safety.
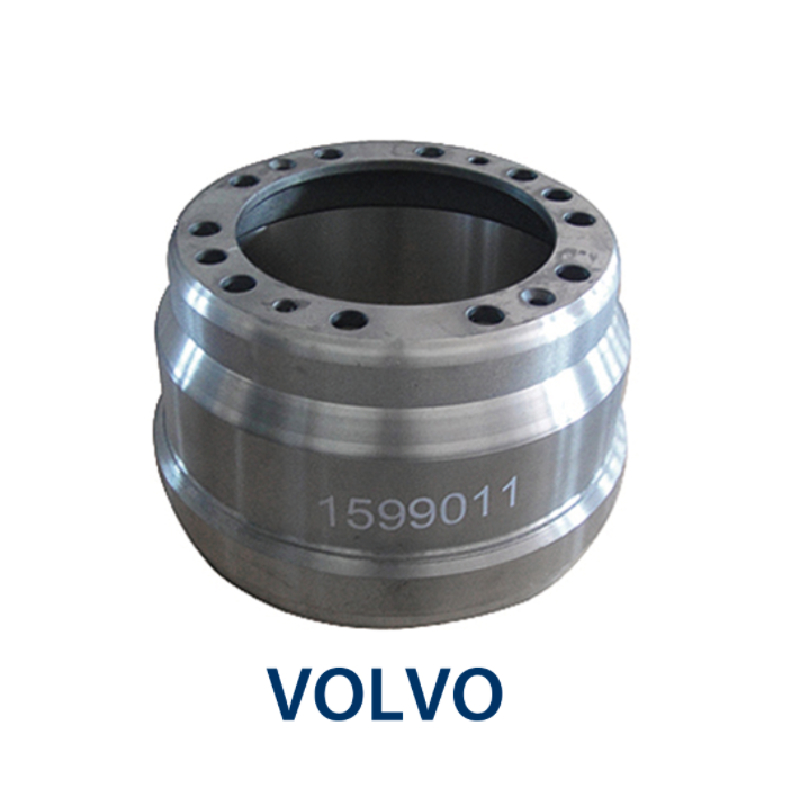
A brake drum forge is an exemplary choice for budding blacksmiths and seasoned artisans alike, due to its affordability and adaptability. The primary component – a discarded brake drum – can often be sourced from automotive repair shops or scrapyards. These robust cylinders are ideally designed to withstand high temperatures, making them a perfect candidate for a beginner's forge.
To start, ensure you have a clean and structurally sound brake drum. Any imperfections, such as significant rust or cracks, can compromise the forge's integrity and should lead to the selection of a different drum. Place your brake drum on a stable surface, such as a sturdy metal stand or a stack of firebricks, ensuring that it is secure and level to prevent any accidents during operation.
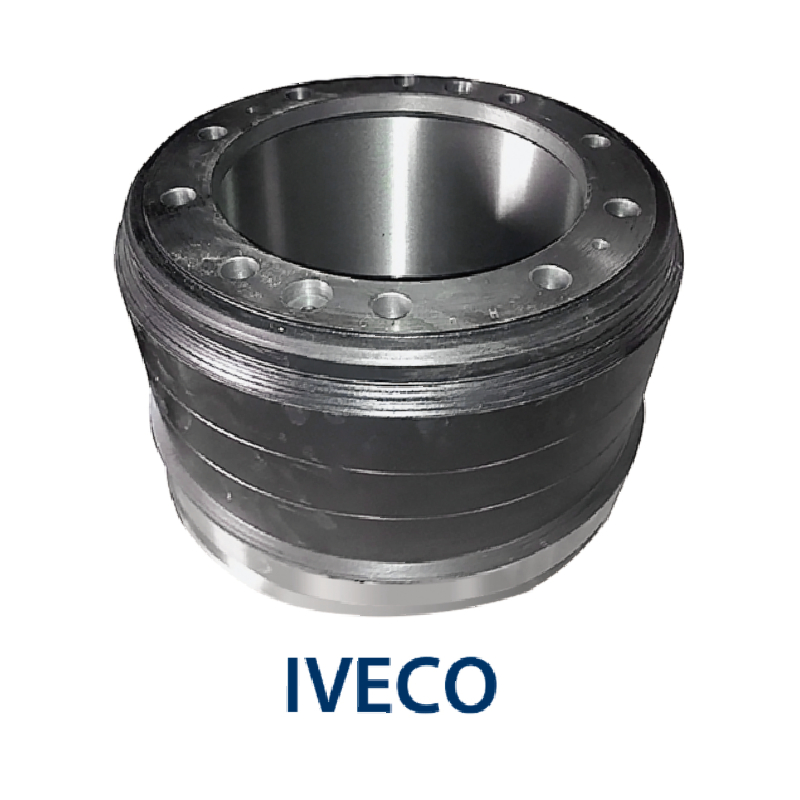
For optimal air supply, the heart of any forge, incorporate a tuyere—a pipe through which air is blown into the forge. Affix the tuyere to the drum's base with welds or bolts, ensuring a snug fit to prevent air leakage. Attach a blower or a source of air pressure, such as a hairdryer or a dedicated forge blower, to the tuyere, allowing for precise control over airflow and temperature regulation.
The lining of the forge is crucial for maintaining high temperatures and protecting the brake drum from thermal shock. Refractory cement, known for its impressive heat resistance, should be used to coat the interior of the drum. Apply a thick layer evenly, ensuring full coverage, and allow it to dry and cure according to the manufacturer's instructions. This process insulates the forge, enhancing its efficiency and prolonging the life of the brake drum.
how to build a brake drum forge
Fuels such as charcoal or coke are recommended for use within a brake drum forge due to their high burning temperatures and availability. Fill the forge with your chosen fuel, adequately covering the tuyere to prevent air blockage yet ensuring ample space for airflow and combustion.
Safety cannot be overstressed when working with forges. Protective gear, including gloves, safety glasses, and a sturdy apron, is mandatory. A nearby bucket of sand or fire extinguisher is a prudent precaution against accidental fires. Moreover, proper ventilation is crucial in preventing the buildup of harmful gases produced during the burning process.
Hands-on experience remains an invaluable teacher. Practice consistently, familiarize yourself with the forge's quirks and capabilities, and soon you'll master the art and science of blacksmithing. As you advance, you might incorporate additional features, like a hood for smoke ventilation or infrared thermometers for precise measurement of metal temperatures, further expanding your forge's capabilities.
Constructing a brake drum forge not only provides an affordable entry into blacksmithing but also serves as a personal testament to innovation and craftsmanship. By following time-tested procedures, maintaining safety standards, and embracing learning from each forging session, you establish a foundation built on reliability and expertise—key principles that stand the test of both time and industrial evolution.