Building a forge using a brake drum is an innovative and cost-effective way for hobbyists and aspiring blacksmiths to begin their journey into metalwork. A brake drum forge is not only affordable but also efficient, using readily available materials to create a functional forge. This guide provides step-by-step instructions, grounded in personal experience and expert advice, to construct a reliable forge from a brake drum.
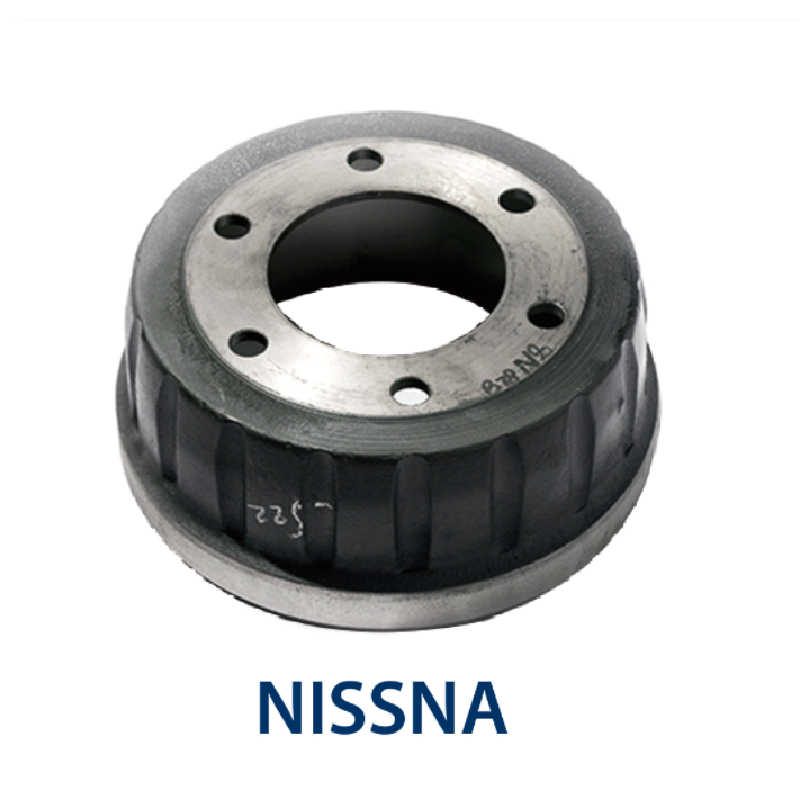
The initial step involves selecting the right brake drum. Opt for a large, heavy-duty drum, commonly sourced from trucks or large vehicles, as these provide a sizable workspace and retain heat effectively. Once acquired, ensure the drum is clean and free from rust or debris. This preparation step is crucial as it extends the life of your forge and enhances safety.
Next, consider the structural base for your forge. A sturdy, fireproof table or stand is essential for stability and safety. The forge will become extremely hot, so using fire bricks or a steel table is recommended to prevent fire hazards.
Weld or bolt the brake drum securely to the base. This connection must be robust to withstand the vibration and movement of forging activities.
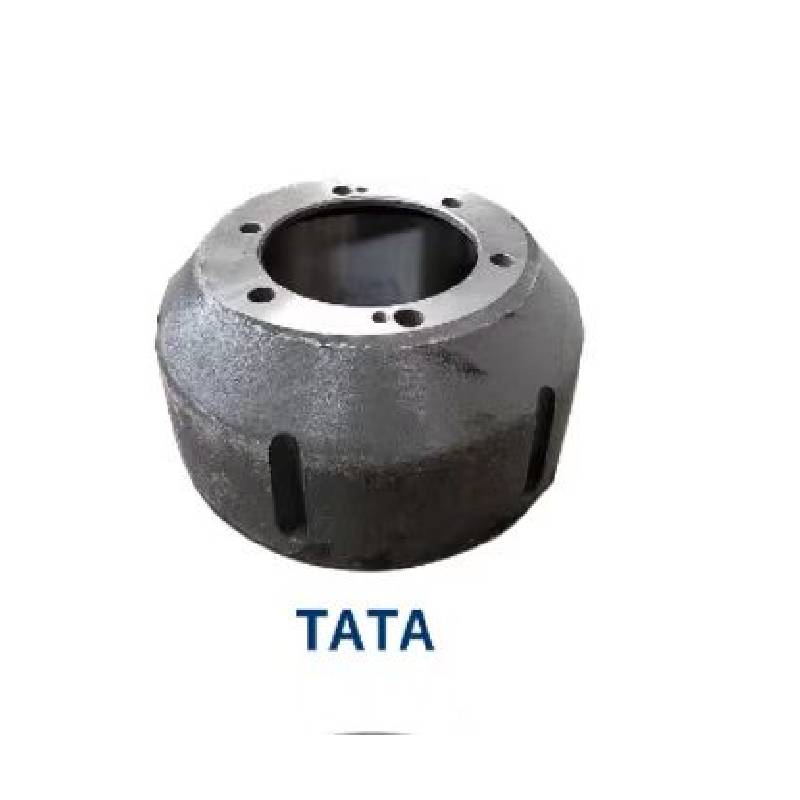
Airflow is integral to maintaining the high temperatures necessary for metalwork. Thus, incorporating a reliable air source, such as a hand-cranked blower or an electric fan, is vital. Drill a hole at the base of the brake drum, attaching a pipe that connects to your air source. This setup creates a 'tuyere,’ a device that injects air into the forge to maintain and control the fire's intensity. Ensure the pipe is made of metal to withstand high temperatures, and adjustability is key for managing airflow with precision.
Safety is paramount when constructing and using a forge. Equip yourself with heat-resistant gloves, safety glasses, and a leather apron to prevent burns and injuries. Additionally, maintain a fire extinguisher nearby as a precautionary measure. The working environment should be well-ventilated to avoid the toxic effects of prolonged smoke and fume exposure.
how to build a forge from a brake drum
Upon completion of these steps, fuel selection is the next consideration. Coal, coke, or even hardwood charcoal can be used to fuel the forge. Each option has unique burning characteristics and heat outputs, so experimenting will help determine what best suits your forging needs. Position the fuel within the brake drum, leaving space for the airflow to reach the heart of the fire.
In terms of use, light the fuel carefully and start the air supply. Initially, a slow air feed is recommended to gradually increase the forge's temperature and prevent any structural damage. The brake drum forge should reach optimal forging temperatures in about 20-30 minutes, allowing you to then introduce metal objects for heating and forging.
Regular maintenance will extend the life of your brake drum forge. Remove accumulated ash and debris after each session, checking the drum for signs of wear. Over time, repeated exposure to high heat may naturally degrade the drum, so inspection and occasional replacement are necessary for sustaining a safe and effective forging setup.
By following these expert steps, you harness the creativity and ingenuity of traditional blacksmiths in creating a functional forge from everyday automotive parts. This project not only saves costs and resources but also provides a fulfilling entry into the craft of metalworking, resonating with both historical techniques and modern practicality.